Kingmans Equation Explained
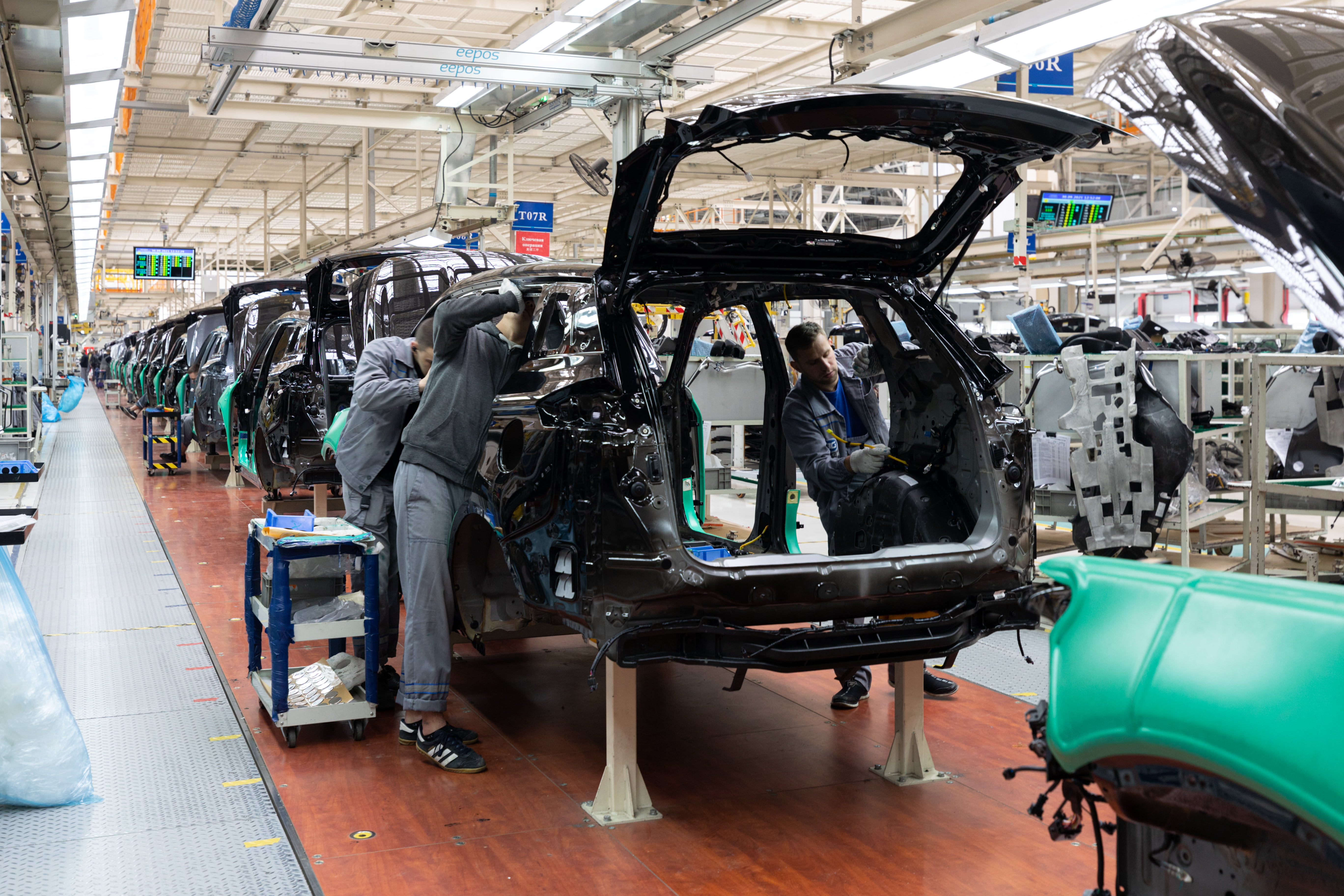
In Lean, Six Sigma, and operations management, one simple truth holds across industries: variability in your process creates queues and delays. Kingman’s Equation - also known as the VUT Equation - helps you quantify this effect and better manage it.
Originally developed for queueing theory in computer systems, the equation is now used to improve flow in manufacturing, healthcare, logistics, and service operations.
Let’s talk about:
- What Kingman’s Equation is
- When and how to apply it
- Key time concepts: Lead Time, Takt Time, Station Cycle Time, and more
- A clear example with real numbers
Key Definitions
Term | Definition |
---|---|
Lead time | The total time from customer order to delivery (external) or the total time from start to finish of an internal process (internal). |
Takt time | The rhythm of production needed to match customer demand (Available time ÷ Demand). |
Planned cycle time | The target time planned to produce each unit (ideally ≤ Takt time). |
Pitch time | The time to complete and move one container of units: (Takt time × container quantity). |
Station cycle time | The time between the completion of two consecutive units at a workstation. |
Process Time (tp) | The average hands-on time to process one unit at a workstation (excluding waiting). This is the tptp used in Kingman’s Equation. |
So why is it also called “VUT Equation” anyway?
Because it shows how Variability (V) and Utilization (U) together with Processing Time (T) drive waiting time.
As U approaches 100%, waiting time increases exponentially. And the more variability (in arrivals or processing), the longer the queue; regardless of process speed.
In other words Kingman’s Equation is often called the VUT Equation because it links:
- V = Variability
- U = Utilization
- T = Processing time
into a simple model of waiting time.
Formula
Where:
- U = Utilization = (Arrival Rate / Service Rate)
- Cₐ = Coefficient of variation of arrival times (σ / μ)
- Cₛ = Coefficient of variation of service times (σ / μ)
- Process Time (tp) = Mean processing time for one unit
Example: Assembly line queue build-Up
At an electronics assembly line, the SmartKettle X is produced across six stations.
Station 4 handles installation and testing of the heating element. The standard process time at Station 4 is 5 minutes per unit.
The takt time for the entire line is 6 minutes; meaning that one unit should be completed every 6 minutes to meet customer demand.
In normal operation:
- Process time = 5 min/unit
- Arrival rate = 10 units/hour (one every 6 min)
- Service rate = 12 units/hour (one every 5 min)
- Utilization (U) = 10 / 12 = 0.83 (83%)
- Initial waiting time ≈ low; line is balanced.
For the first hour, flow is stable.
A variability event
At the start of the second hour, a small issue occurs: a batch of kettles arrives with a stiffer gasket, causing installation to take 7 minutes instead of 5 for the next few units.
Updated numbers:
- Process time = 7 min/unit
- Service rate = ~8.6 units/hour
- Utilization (U) = 10 / 8.6 ≈ 1.16 → over 100%
Since the arrival rate remains fixed (every 6 minutes), the station now falls behind:
- After 1 unit → 1 min late
- After 2 units → 2 min late
- The queue begins to build.
Compounding delay
By the 4th delayed unit:
- 4 kettles have arrived in 24 minutes
- Lisa has only completed ≈ 3 units
- Queue length = 1 unit
- Utilization (U) remains > 1; impossible to catch up unless arrivals slow down or process variability is corrected.
Even once the gaskets return to normal, Station 4 is still behind by several minutes, causing upstream stations to pause, as they can’t offload finished units.
Queue impact after 5 hours
If this level of variability (temporary but recurring) repeats each hour, the backlog compounds.
Assume:
- For each problematic batch, Station 4 runs at U ≈ 1.16 for 15–20 min/hour
- Average deficit ≈ 1–2 units/hour added to the queue
After 5 hours:
- The queue at Station 4 could easily reach 5 to 10 units waiting
- Equivalent to 25–50 minutes of buffer just sitting idle
- The entire line output slows, and overall lead time increases significantly
Reducing Variability (Cₐ, Cₛ) to Stabilize Flow
Continuing this example: Initially:
- Cₐ = 1.0 (high arrival variability)
- Cₛ = 0.5 (moderate service variability)
Now assume the team improves standard work and stabilizes the supply:
- Cₐ = 0.3
- Cₛ = 0.2
Result: Waiting time drops from 15.6 min → 1.6 min, purely by reducing variability. The same utilization (U = 0.83) now results in much faster flow.
A well-balanced line with low variability can tolerate occasional issues and minor spikes in U without triggering runaway queues.
Visual: Queue build-Up over time
Kingman’s Equation Visualizer
Results
Utilization (U): 0.75
Average Waiting Time: 15.00 min
Total Lead Time: 20.00 min
Values above 500 min are shown as "Wq > 500" — theoretical infinity when Arrival Rate = Service Rate. Extreme points shown in red.
Summary
Kingman’s Equation gives us a powerful way to predict and manage waiting times caused by process variability and utilization.
Key Takeaways:
As utilization (U) approaches 100%, queues grow exponentially; even small variability becomes costly.
Reducing variability (Cₐ and Cₛ) has a huge impact on lead time and flow; often more than simply speeding up the process.
A well-balanced, stable process can absorb occasional variability without runaway delays.
Use the VUT Equation to model, improve, and control your operations; whether in manufacturing, healthcare, logistics, or services.