Little’s Law and why your line isn’t faster just because it’s fuller
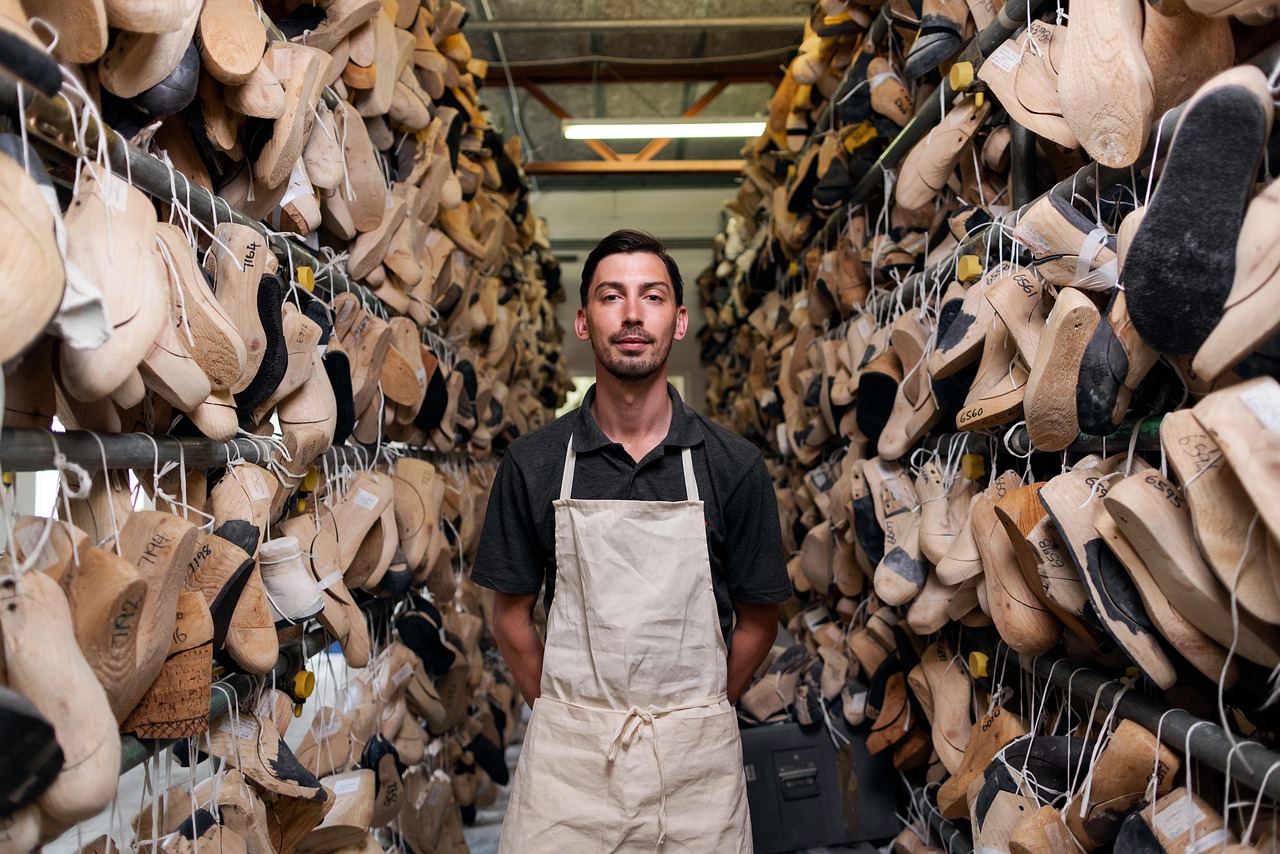
Understanding the link between work-in-progress, lead time, and throughput
The packaging team is busy, forklifts are moving, and pallets are stacked. Yet customer complaints about late deliveries keep rolling in. Sound familiar?
This is where Little’s Law becomes more than a formula. It becomes a system mirror.
Why some busy systems still underdeliver
Little’s Law connects three core parts of any production or service system:
It describes how long something spends in the system, based on how many items are being processed and how fast they are completed.
Unlike complex simulation tools, Little’s Law works on napkins, dashboards, and whiteboards. When used consistently, it reveals why “more work” often leads to less flow.
What the formula actually means
Let’s break the variables down.
Lead Time: How long it takes for a single unit to go from start to finish
Work in Progress (WIP): How many units are currently being worked on, across all steps
Throughput: How many units leave the system per time period (per hour, per shift, per day, etc.)
Here’s how it behaves:
If throughput is stable and WIP increases, lead time grows
If WIP stays stable but throughput increases, lead time shrinks
To reduce lead time, lower WIP or raise throughput
This relationship is mathematical, not optional.
Example: Heel Yeah and the vanishing sneakers
So Heel Yeah, a fictional shoe design and manufacturing company, had a growing backlog in its custom sneaker line. Customers were told production took five days, but real lead times were averaging closer to twelve.
A quick walkthrough showed the system looked busy. Cutting tables were full, stitching teams were stacked with work orders, and final assembly had no empty racks. No one was idle.
After a data pull, the production planner charted the actual numbers:
WIP = 480 pairs of shoes (in various production stages)
Throughput = 80 pairs per day
So according to Little’s Law:
But the lead time seen by customers was 12 days, not 6. Why?
WIP was not evenly distributed. Most of the inventory sat in queues between stations, not in active production. For example, over 200 pairs were stuck waiting for eyelet punching, which only had one operator.
They took three steps:
Introduced a WIP cap of 60 pairs per process step
Balanced staffing around the bottleneck
Built a daily visual flow board to show where inventory was held
Within three weeks:
WIP dropped to 320 pairs
Throughput remained stable at 80 per day
Lead time dropped to 4 days
On-time delivery rate improved by 28 percent
They didn’t speed anything up. They just made flow visible and limited overload.
Best practice tips
Use visual WIP limits: Even tape on carts helps build flow habits
Measure at system level, not department level: One team’s efficiency can hide another team’s blockage
Talk in units, not just hours: Use throughput language to ground conversations
Look for the real constraint: Adding labor where flow is already stuck creates more WIP, not more output
Key takeaways
Little’s Law gives a practical way to track flow health
Lead time grows if WIP rises faster than throughput
Faster output requires better flow, not more effort
Tools like WIP caps and flow boards make the law visible
Use the formula regularly to spot overload before it hits the customer